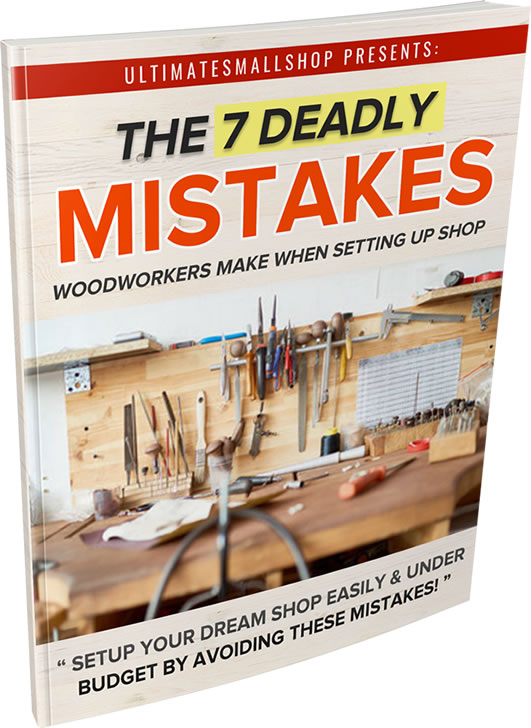
1 FAILURE TO CONSIDER WHAT YOU ACTUALLY NEED
If you are looking to set up a shop on a budget and are doing so for the first time, you need to first consider what space do you have available for your shop and what you are hoping
to make in your shop, not necessarily in that order.
For example, a crafts person looking to make some gifts like boxes is different from a crafts person looking to set up a business selling gifts in quantity to make a living.
A DIYer person with a home shop looking to make cabinets, tables, and furniture for their home is different from someone crafting the same things for customers. Some people are looking to be a woodworker primarily in the old school of hand tools while others are primarily a power tool person with little interest in hand tools. Do your interest lie in fine woodworking like wood carving, lathe turning, scroll sawing…or carpentry or furniture building or just furniture restoration?
The other significant consideration is what space is available. It is always kinder on the budget to use the space you have. This is sometimes the first consideration. A novice might ask what kind of woodworking can be done in the available space? Is it a basement, a garage, a “bedroom” in an apartment? Is the garage or basement space small, medium or large? Is it quite narrow but long, or a medium or large open room?
2. BUYING TOOLS THAT YOU DON’T NEED
For efficient space planning, it is important not to go crazy and buy large power tools or equipment. The ability to use floor space more efficiently must be considered. As an example my table saw has the ability to mount a router. Also, there are many table saws which are portable and generally smaller in size. It’s a good idea to consider them for small spaces.
Even better are rolling work stations and multi tool tables. Now you should buy tools as you need them. Consider this:
Does this tool meet my need today?
If it does, how long will I take to outgrow it, if ever?
If you don’t need them yet, you don’t know if you will need them in the future and you might just end up wasting money.
As for me, I will always recommend hand tools first. A few simple (and inexpensive) hand tools: chisels, a mallet, a saw or two. There. You haven’t even spent $100 and you can get started making fine crafts.
Eg: Mallets and Beveled Chisels:
A set of sharp beveled chisels is often great to have in your toolbox.
You can cut your dovetail joints, add decoration to your piece, and hundreds of other uses.
Paired along with a rubber mallet, you don’t need a circular saw.
Hand sanding:
Instead of buying a dremel rotary tool to sand, you could sand your projects by hand. Hand sanding takes a lot of time and hard work, but it’s one of many skills that can help you improve as a woodworker.
Work With a Hand Saw:
Power saws can be frightening to use. Who doesn’t fear to lose their thumb with those things? Using a hand saw may take a bit of elbow grease, but it’s certainly a safer alternative than a circular saw or a jig. As long as your hand saw is sharp, your cuts will be too.
For the best “bang for the buck” power tool, my vote goes to a good circular saw and guide. It is useful for a lot of dimensioning and edge jointing and panel jointing.
To find out how to get deep discounted tools that you actually need, check out Ultimate Small Shop My guide will give you multiple lists of various budgets and exactly WHAT tools to get and WHERE to get them at deep discounts
3. OVERSPENDING ON TOOLS
There was a point in my woodworking in which I strongly believed in the “buy-as-much-of-a-tool-as-you-can-afford” theory. But when reality sets in, (several months after you have bought the tool) you realize that this might not be true for all of your purchases. At this point, it’s easy to say “Maybe I didn’t need that much of a tool for what I do” and if your are thinking that now about something you own, you are probably right.
I have purchased more tools than I care to mention based on comments from the professionals whose articles we read in woodworking magazines everyday. Some of them only recommended one particular brand based on limited knowledge and the assumption that a given manufacturer’s quality is present throughout their entire line of tools. Few cabinet makers recommend tools based on affordability.
And lastly, some professional’s recommendations are based on which manufacturer gives them sponsorship (in other words, free tools). You may enjoy woodworking as much as they do but we can’t devote as much time to it because woodworking is not what we do for a living. I’d guess that few of the high and mighty professional woodworkers go home from a long day at work and head for the basement woodshop. Keeping this in mind, remember the difference in time spent using the tools they own compared to the hobbyist woodworker. Our tools do not need to be identical to theirs. Most of us are on a tight tool budget that requires us to make smart purchases based on what we need as hobbyist woodworkers.
It is said that hindsight is always 20/20 and it’s something you just can’t argue. So let my hindsight be your foresight and maybe the marketing efforts of tool companies and the holy rollers of the woodworking world can be put at bay while you make the right decisions in your tool buying future.
4. ASSUMING YOU NEED A LARGE SPACE FOR YOUR SHOP
Don’t be discouraged if you do not have adequate space.
The smallest functioning shop I’ve seen is 36 square feet. It consists of a “workbench” that stands18 inches tall. So, you could setup a shop and start woodworking if you have more space than 36 square feet!
I would recommend going for 10×18 if you do have more than 36 square feet of space.
Why that dimension?
Personally, I like to have enough space to be able to cut a 4’x 8′ sheet of plywood or medium-density fiberboard (MDF).I need 8′ of clearance for the blade on my table saw and 8′ of clearance behind it.
Most big box retailers who carry lumber, such as Home Depot or Lowe’s, will do some cutting for you. I have used those services, but I really prefer to buy my sheet goods as full sheets.
One thing that makes any shop a little more user-friendly is to have your major equipment “moveable.” This is a requirement if you have your shop in a garage, sharing space with the family vehicles. It is useful, too, in the basement if your basement is crowded. At a minimum, I recommend having a mobile table saw.
For such space spaces, it would be ideal to have a 4-in-1 type of workstation that maximizes the use of your space.
You can build your own very small woodworking bench that can incorporate your table saw, router and scroll saw all using the same bench top. Each tool folds down or stows below the bench top to make room for the other tools.
5. SETTING UP SHOP IN A BAD LOCATION
There are great places to setup a shop and there are not so ideal places and it all depends on your needs. Finding the best location can be challenging and each space comes with its advantages and disadvantages; these, too. My guide Ultimate Small Shop will explain more in-depth.
Here’s a quick summary.
If you’re working with heavy machinery or are noise sensitive, it is a bad idea to setup shop in the attic. Access to an attic workshop is mainly upwards in a narrow stairway. This may make getting tools and machinery into the basement quite difficult. Moreover, attic floors become inadequate to bear heavy woodworking machinery and tools. Noise can be transmitted to the entire house through floor vibrations as you work.
Basements are great for heavy machinery and noise control but it also present access challenges. And if your basement floods after the rain, it not wise to setup shop.
If you have a central furnace in the basement, you have got to be extra aware of the accumulation of sawdust to avoid a fire hazard.
If you like to know all available spaces you can setup a shop, the pros and cons of it, check out UltimateSmallShop.com
6. NOT GETTING THE MOST OF YOUR SPACE
Getting the most out of a small shop takes more than just having the right tools set in the right places. One of the keys to getting a modest space to work really well is to ensure that all its work surfaces enjoy a sweet synergistic relationship with one another.
In my shop. this means that the table saw serves as the benchmark height for every other horizontal surface within an B’ radius of the blade. An outfeed table, a side table (which holds an inverted router and allows me to use my table saw fence as a router table fence) and the top of the jointer fence (a length of wood bolter to its metal fence) surround the saw and are set to that benchmark.
To further encourage synergy, I also built my main assembly bench and a storage cabinet to the same height.
Now none of the tables get in the way of one another when I’m working with large components and materials. In another part of the shop, I built a workbench next to the drill press at the same height as the drill press table to provide additional support when drilling long boards. Similarly, my sliding compound miter saw gets a big helping hand from a pair of tool storage cabinets that I set to either side of the saw, their top surfaces level with the saw table.
The bottom line is that I seldom. if ever, have to move furnishings around (though sometimes I do have to clear them of) in order to work with large pieces of stock. My shop furniture is all one happy family working together to keep me happy.
7. FAILURE TO ACCOUNT FOR VENTILATION AND DUST
A lot of woodworkers who are starting their first shop usually have inadequate ventilation and dust management
It’s necessary in order to breathe easy and feel good. Good air circulation will whisk away adhesives and fumes from your finishes. The air is filled with fine dust, as well as smoke, that is generated during various operations like shaping. It needs to be removed and replaced with fresh air.
Exposure to wood dust has long been associated with a variety of adverse health effects, including dermatitis, allergic respiratory effects, mucosal and nonallergic respiratory effects, and cancer. Contact with the irritant compounds in wood sap can cause dermatitis and other allergic reactions.
Whether it’s a broom and dustpan or a state-of-the-art central collection system, every woodworker needs to have some kind of strategy for dealing with wood waste in the shop. Of course, some of these methods produce better results than others in terms of fire safety, cleanliness and respiratory health.
But regardless of the kind of dust control or collection equipment you have in your shop, sawdust can still become a problem unless you learn to use your equipment effectively.
Keeping dust out of a fresh finish can be a major accomplishment in a typical small, single-room woodshop. Unfortunately, sucking air through the shop to remove finish fumes tends to stir up wood dust. This potentially pulls in pollen, insects, and dust from the outdoors.
To learn more in detail, visit UltimateSmallShop.com
Our website is supported by our users. We sometimes earn affiliate commissions when you click through the affiliate links on our website
Click Here to download your free 440 page Woodworking Book with 50 free Plans